Virginia Tech holds rich resources in the field of metal 3D printing, giving researchers and learners access to innovative projects and partnerships.
A diverse set of tools for metal additive manufacturing is rare in an academic setting, but Virginia Tech has amassed an impressive collection on its Blacksburg campus. As new technologies are developed and deployed, the university’s College of Engineering continues to be a rallying point for these innovations.
Virginia Tech has established itself as a global leader in the additive manufacturing (AM) field at large, having recently been identified as one of the Australian Strategic Policy Institute’s top 20 global institutions in the field based on various publication metrics.
In the world of additive manufacturing – commonly called 3D printing – working with metal is almost exclusively an industrial job. Rendering projects in metal requires machinery that is larger and more expensive than the typical desktop polymer printer, not to mention the expert-level training required for safe operation. As a result, most universities tend to only have one or two of these large machines available to their community.
Virginia Tech has five, made possible by the funding of industry and federal agencies that value the university’s research and seek to equip the future workforce with experience and knowledge of those machines and processes.
A complete set of tools
Metal additive manufacturing at Virginia Tech extends beyond any one program or discipline. It’s distributed throughout campus, with some machinery available for public use. Hokie machines represent these methods:
- Binder jetting involves selectively inkjetting a binding agent (something like a glue) into a layer of fine metal powder to define a single part layer. The machine then spreads another thin layer of loose but tightly packed powder across the previous layer, and the process repeats layer by layer until the object is complete. To fully fuse together the metal powder, the piece must be heated upon completion. This step, called sintering, coalesces the individual powder particles together to provide the requisite density and strength for final application. The part will shrink as it heats, so a designer must account for the piece’s smaller size and scale up accordingly. Binder jetting’s use of inkjet nozzles to form the part make the method extremely scalable and often useful in producing parts for automotive, oil and gas, and even jewelry applications.
- Laser powder bed fusion is similar to binder jetting because it also spreads layers of fine powder. But instead of directly applying a binder to the powder, a laser selectively melts the metal powder in a process similar to microscale powder welding. Because the parts are fully dense at completion, they can be used immediately and do not require an additional sintering step. Powder bed fusion is the preferred method when material performance and precision are critical, such as in aerospace applications.
- Directed energy deposition (DED) is the oldest method of additive manufacturing with metals. This method works much like welding, where metal is channeled directly into an energy source (e.g., a welding arc or a laser) in either powdered or wire form. DED can render very large metal parts at a high throughput. Post-process machining is often used to achieve the surface finish and details required of the final application. DED is unique because it can also be used for repairs or upgrades of current pieces, as a rotating print head can make angular deposits onto an existing piece. Virginia Tech’s unique hybrid wire arc additive manufacturing DED workcell enables the operator to both deposit metal and do machining within the same machine.
- The upstart new kid on the block, additive friction stir deposition (AFSD), is a novel method of metal AM proprietary to Meld Manufacturing in Christiansburg. This process doesn’t use powders or binders, nor does it reduce metal to a liquid state. Instead, it uses metal rods that are pushed through a hollow rotating tool, causing the metal to soften and deform. In that softer state, the metal can be shaped and printed. Since the metal never reaches the temperature to liquefy, this method is much more convenient for metals that don’t respond well to melting.
- Bound metal extrusion is similar to common polymer extrusion AM machines found in desktops and garages across the country. However, instead of melting and extruding plastic, these machines extrude a composite material made of a wax-like material and metal powder. Once printed, the parts are treated to a sintering step, much like the one used in binder jetting, to remove the binder and to coalesce the metal particles into a cohesive part.
Each of the methods comes with its own set of benefits, and results will vary across applications. Some methods, such as the stirring technique, are extremely fast and well suited to producing large, solid metal parts. Binder jetting is often used to make a large batch of small parts quickly. Metal extrusion can make functional prototypes and models that require the properties of metals.
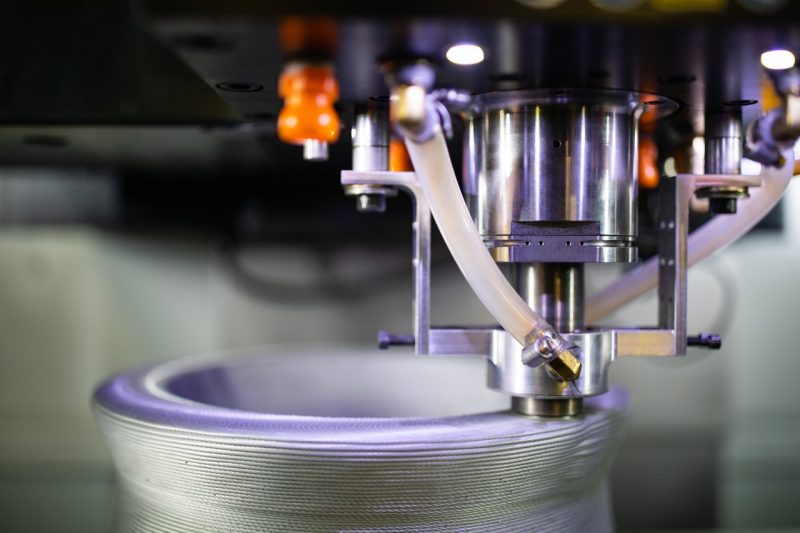
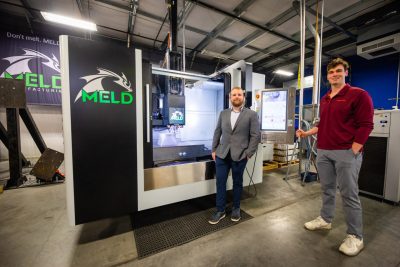
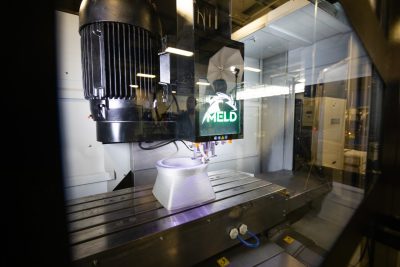
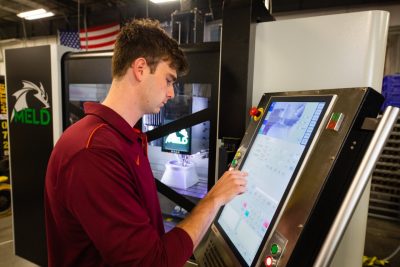
A growing team of experts
Taking possession of such powerful tools is a moot point without the expertise to deploy them. Virginia Tech has steadily grown its personnel ranks to meet the increasing need to learn and teach these new technologies.
Associate Professor Hang Yu, a researcher in the Virginia Tech Department of Materials Science and Engineering, is a recognized authority in the additive friction stir deposition technique developed by Meld, and has authored a textbook about the method. Yu is the primary investigator for a Defense University Research Instrumentation Program (DURIP) grant, awarded earlier this year, that was used to place one of Meld’s AM machines in his lab. Yu has also received a DARPA Young Faculty Award to study autonomous options for metal AM under austere conditions.
Publicly available, the Newman Library Prototyping Studio has an extrusion printer capable of printing stainless steel, copper, nickel-based superalloys, and other metals. Staff members are available to help users of all experience levels design and develop projects for the machine.
By far, the largest collection of AM tools resides in the Design, Research, and Education for Additive Manufacturing Systems (DREAMS) Lab directed by trailblazer Chris Williams, L.S. Randolph Professor of Mechanical Engineering.
Williams’ team has been working in metals for more than a decade, shaping a wide range of materials. DREAMS Lab metal AM facilities include binder jetting and DED. The DREAMS Lab has also worked with Alan Druschitz at Virginia Tech’s Kroehling Advanced Materials Foundry to create 3D-printed sand molds that are used to make poured metal forms of complex lattice structures. Williams was also the primary investigator for a DURIP grant that brought metal laser powder bed fusion to campus; the system is housed in the shared “Future Manufacturing Lab” thanks to support from the Institute for Critical Technology and Applied Science.
“We have lots of ways to get to complex, three-dimensional structures made out of metal at Virginia Tech,” said Williams. “It’s unique for a college campus to have access to the methods available here. From an educational standpoint, it’s also important because we equip students with a unique set of manufacturing skills. As a land-grant institution, our mission is to spread these emerging technologies to the region, the Commonwealth of Virginia, and beyond.”
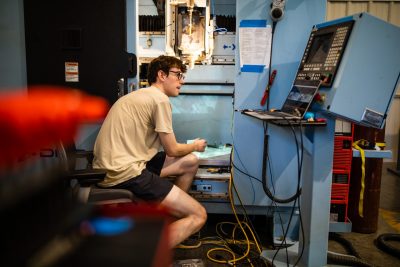
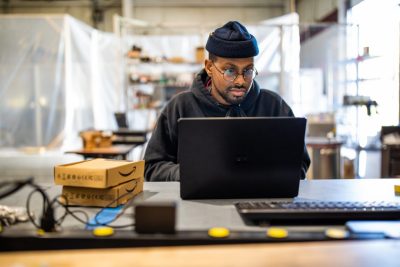
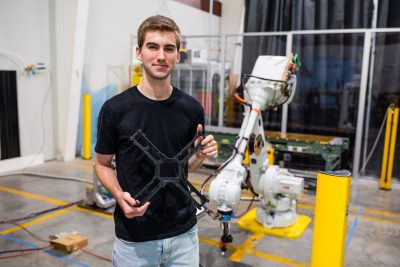
Virginia Tech research has gone far beyond making things out of metal. As the capabilities of metal printing have multiplied, so have the questions. Researchers are busily investigating how to make the methods of metal AM equal in quality to more traditional methods such as casting – and exploration funding has followed.
Yao (Yolanda) Fu, an assistant professor in the Kevin T. Crofton Department of Aerospace and Ocean Engineering, received a 2022 CAREER grant from the National Science Foundation to compare the impacts of fatigue in metals produced by both additive and traditional methods. Her research investigates the unique strengths of 3D-printed alloys under both normal and corrosive circumstances, focusing on the laser fusion method.
Professor James Kong in the Grado Department of Industrial and Systems Engineering has developed a method to fine-tune the precision of laser fusion. As part of the Multidisciplinary University Research Initiatives Program sponsored by the Office of Naval Research, Kong's team has developed a set of sensors attached to a laser fusion machine that give them the ability to adjust as the additive process occurs. By analyzing factors during the process, such as the dimensional accuracy of the printing, laser spot speed, and laser power, researchers can more precisely control the piece they produce.
Prahalada Rao, an associate professor of industrial and systems engineering, also garnered an NSF CAREER award to study the integrity of 3D-printed pieces. Rao’s team developed a novel technique to detect flaws in laser-fused pieces down to the fraction of a millimeter. His team is also commercializing a new simulation approach to predict the temperature of the part as it’s being created – the root cause of all errors in metal additives. Their simulation software is 10 times faster than existing approaches, and its development is being funded by the National Science Foundation.
Mentoring new experts
Placing machines on a college campus must ultimately serve the students, and metal printing is no exception. Student researchers are attached to all the resources mentioned here, and the state-of-the-art equipment provides an immersive experience for them with the same equipment they might use in a career. Coursework has also been added to the engineering curriculum that integrates metal AM, taught across departments by experts like Pinar Acar, Yu, and Williams.
Students have also developed their own projects using these resources. When Boeing needed a way to make additively manufactured replacement parts for older planes, the company sponsored a senior design team through the Department of Mechanical Engineering to work on the problem.
“The precision molds that they need to make would cost Boeing half a million dollars for a single part,” team member Ben Nguyen said in an interview on the 3D Printing Nerd. “Boeing was looking towards [DED] to produce parts that are a lot cheaper.”
The team created a usable part optimized for weight precision, plus a method for reproducing more. They did most of the production with a DED machine and completed finer finish work afterward with computer numerical control. Their project received top prize at the Society for Manufacturing Engineers' Direct Digital Manufacturing student competition at RAPID+TCT 2022.
Students who have used Virginia Tech’s state-of-the-art equipment have gone on to careers that sharpen the technology’s cutting edge. A short list of notable alumni include Oak Ridge National Laboratory’s Amy Elliott, GE Additives lead engineers Michael Barclift and Shannon Morman, Naval Surface Warfare Center materials engineer Mackenzie Perry, and Auburn University Assistant Professor Peter Liu, who received an NSF early CAREER award for his AM research, to name a few.
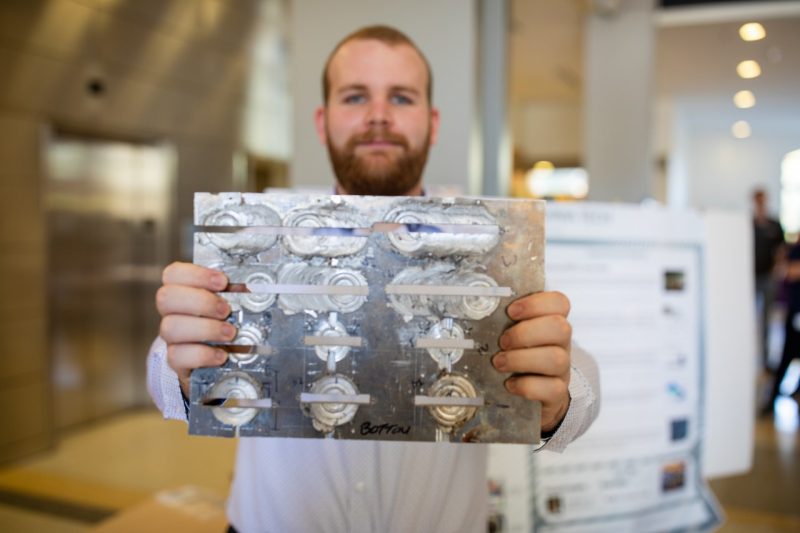
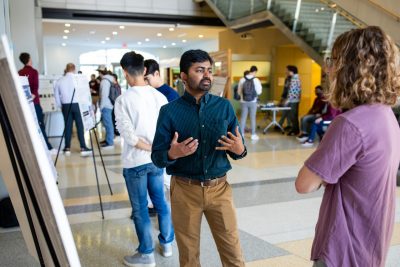
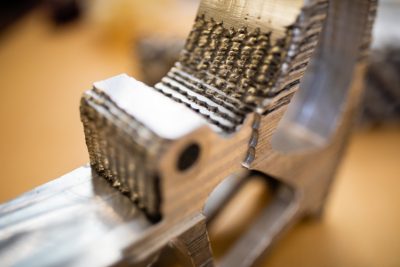
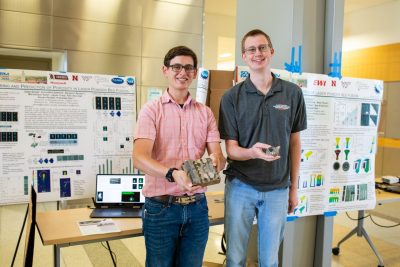
Partnerships for the future
Activating educational facilities for critical applications has generated a passel of partnerships – ones that provide new machinery and also test the limits of tools already in place.
Projects from federal agencies including the National Science Foundation, the Office of Naval Research, the U.S. Air Force, DARPA, and the Defense Logistics Agency, as well as numerous industry partners including Northrop Grumman, Boeing, Collins Aerospace, and the Commonwealth Center for Advanced Manufacturing, have put researchers squarely in the middle of the action for metal AM, and have given students a network of professionals to draw from after completing their education.
One of the most recent inclusions on that list is Meld Manufacturing, creator of the AFSD stirring method. Meld’s headquarters are located just minutes from Virginia Tech’s Blacksburg campus, creating unique opportunities for hands-on collaboration. Nanci Hardwick, CEO of Meld Manufacturing, commented on this critical cross-town camaraderie in a March 2022 interview with Virginia Tech.
“We have a primary relationship and an ongoing relationship with the [Virginia Tech] material sciences department. They're so critical for us because they have expertise,” said Hardwick. “They have one of our machines, and they have world-class characterization equipment. Because this is a new process, our customers need to know a lot of information about the material that we print, and Virginia Tech is helping us get that information.”
Photos and video by Peter Means
If you want to have an impact on our students and faculty like those featured in this magazine, go here to support the College of Engineering. For more information, call (540) 231-3628.