How additive manufacturing is helping a local 12-year-old girl, your golf game, and the exploration of space.
What do fist bumps, customized golf grips, and Kapton have in common?
The short answer: additive manufacturing.
Commonly known as 3-D printing, additive manufacturing is used to fabricate prototype parts and complex forms, by printing them layer by layer. This advancing technology offers applications that benefit diverse industries such as automotive, aerospace, defense, and consumer products to medical, dental, and even recreation.
At Virginia Tech, researchers are using the technology in innovative and helpful ways — resulting in at least three compelling case studies in what additive manufacturing can do to improve lives.
Fist bumps
Josie Fraticelli doesn’t let anything hold her back from doing the things a 12-year-old girl does. She rides a bike, plays softball and the trumpet, swims, and can fist bump.
Josie was also born with amniotic band syndrome. While in utero, the development of her hand stopped. String-like amniotic bands restricted blood flow and affected the development of Josie’s right hand, causing a lack of formation beyond the knuckles. Her parents never knew this was occurring during pregnancy, despite a 3-D ultrasound.
Once Josie was born, her parents Barbara and Tom Fraticelli immediately began to research and found the defect is relatively common—estimated to occur in one in 1,200 to 15,000 live births. Further online investigation also showed the couple that there were a network of individuals that produce prosthetics using 3-D printers. But the production cost is expensive.
Enter Blake Johnson, an assistant professor in the Grado Department of Industrial and Systems Engineering (ISE), who learned about Josie from Barbara, who was also his colleague at the time.
“When Barb told me about Josie, I knew we could help,” Johnson said.
Together they looked over the research she and her husband had found. Johnson, inspired to help based on his related research expertise in additive biomanufacturing, created an undergraduate research project for ISE students to help them apply their knowledge toward design and fabrication of a 3-D printed personalized prosthetic hand for Josie.
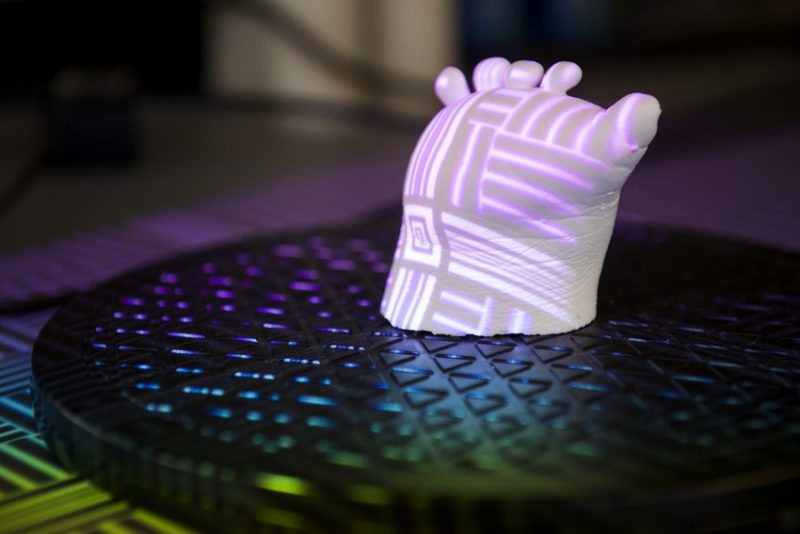
"This was an exciting chance to a create a unique experiential learning opportunity for undergraduate students in the ISE department, while at the same time make a difference in the life of a child from our local community," Johnson said.
Growing up, Josie struggled to grasp objects with her right hand. Still, she adapted to the world around her, despite negative remarks from some of her insensitive peers.
“At a young age, Josie knew she was different from other kids, but didn’t let that stop her from trying new activities or being independent,” Barbara said. “She even tied her shoes earlier than any of her siblings.”
With the goal of providing Josie a functional prosthetic hand, the actual process of creating the hand began by downloading a preliminary digital model from an open-source online database for 3-D printed prosthetics. The students scaled the digital model based on measurements of Josie’s hand that required the prosthetic.
Then the digital model of the hand was uploaded into a 3-D printer that deposited a hard plastic material, layer by layer, ultimately creating the components of the prosthetic hand. The team of four students assembled the hand using additional screws, nuts, and cables.
The end result? An affordable alternative to other prosthetics costing thousands of dollars, using only $20 worth of plastic and $10 worth of assembly material.
Justin Halper, now a graduate student in the department of mechanical engineering, began work on the project as an undergraduate in spring 2016, joined by a team of fellow ISE undergraduate students that included Elena Karakozoff, Nikita Khandelwal, Alex Meholic, and David McIlvain.
“For the initial prototype, I helped with picking the design of the hand and with assembly. Taking courses in Computer Aided Design and Additive Manufacturing helped solidify my understanding of concepts necessary for future prototypes,” Halper said. “Now with more knowledge and experience, I have taken a leadership role with regards to designing the customized aspects of the prosthetic hand and modeling them in software.”
Halper has designed the customized insert that will be in the team’s most recent prototype, combining his CAD skills and additive manufacturing knowledge.
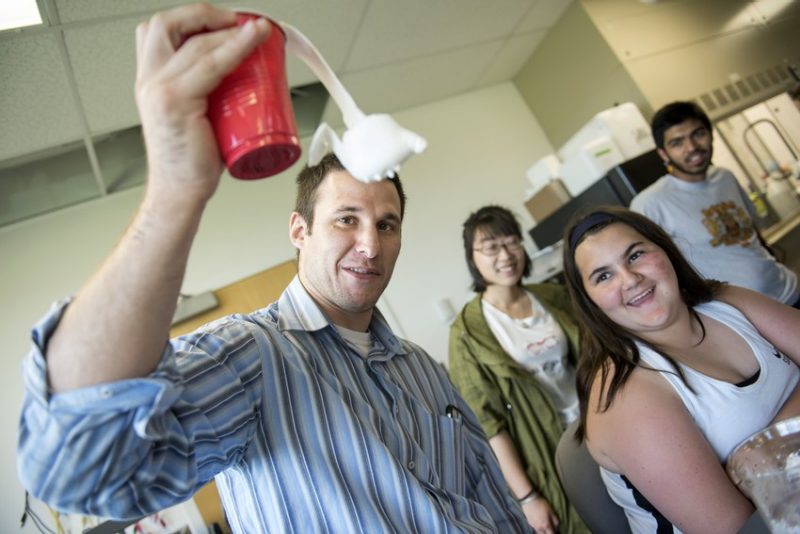
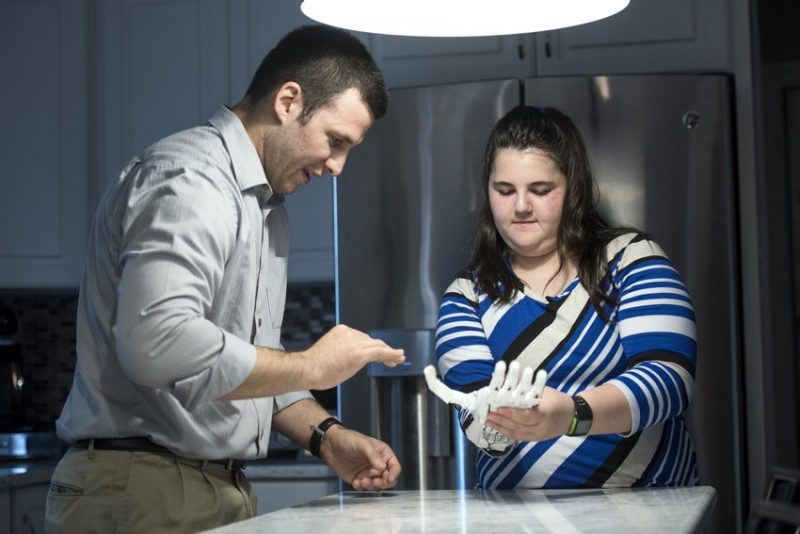
Since being outfitted with the initial prosthetic this past summer, Josie initiates grasping and opening action in the 3-D printed hand through bending and straightening her wrist. Being used to only one hand, Josie had become very independent with it and has had to consciously work to use both hands, instead of one, to perform daily tasks.
The prosthetic hand contains an embedded system of passive mechanical components to transfer Josie’s wrist motion into movement of the prosthetic hand.
“In the beginning, I had to remind her to use it,” said Barbara. “She’s adapted to so much with one hand, it's hard for her to remember to use both.”
Now Josie rides her bike more safely and comfortably and can pour herself a glass of milk without spilling.
This fall, Johnson and his students began work on a next-generation ‘personalized’ prototype designed specifically to match the geometry of Josie’s hand, which required the imaging of Josie’s hand using 3-D light scanning instruments.
“The end goal is to develop additive manufacturing techniques that enable the anatomical matching between materials and tissues, such as in the case of form-fitting and ‘personalized’ biomedical devices,” said Johnson.
Halper plans to see this project through. For him, the hands-on experience will only get better.
“In class we usually learn how to do things where we assume everything is optimal and everything goes right. With this project, several bottlenecks have come up that require outside-of-the-box thinking. There is no set formula or equation that will automatically lead to the perfect solution,” Halper said. “This is how it is in the real world, and the project has provided me with great problem solving experience.”
From Halper’s perspective, the best part is that he gets to see a tangible result for the hard work.
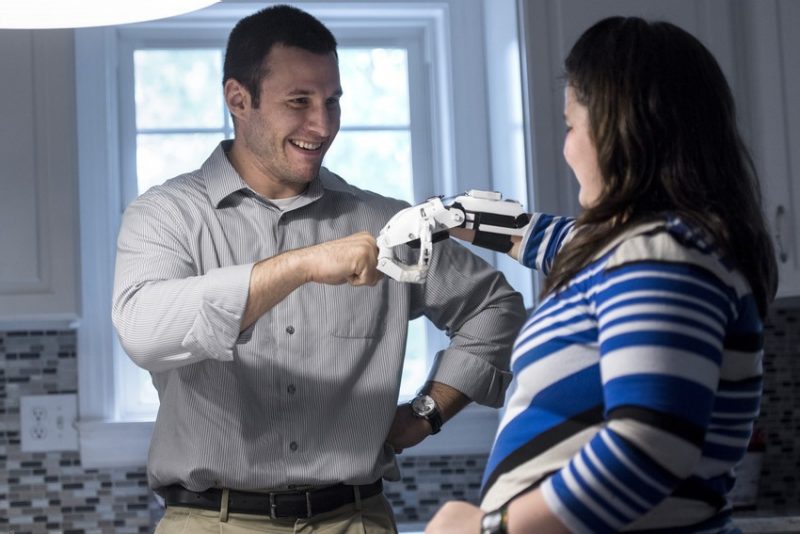
“As students, sometimes we get caught up in grades and letting that serve as a result of our hard work. In this case, it isn’t just about a grade, but rather something much more rewarding in helping to make someone else's life better,” Halper said.
As for Josie, her life with the use of two hands should get easier. As she grows, the hand can easily be scaled up using the same process and materials. But as technology advances, so will 3-D printed prosthetics.
For now, Josie says she’s happy she has the use of two hands and can fist bump with either one.
Golf grips
A Virginia Tech student engineering team created a customized 3-D printed golf grip that uniquely conforms to individual golfer's hands to guide correct placement each time he or she picks up a club.
To create this game-changing golf grip, the team made a clay mold of hands in the correct grip position, scanned the mold, and converted the image to a 3-D Computer Aided Design model before printing.
The result is a grip that can be slipped onto golf clubs and used as a non-tournament aid for players to help build muscle memory and achieve the desired consistent, correct grip without the need for a professional trainer.
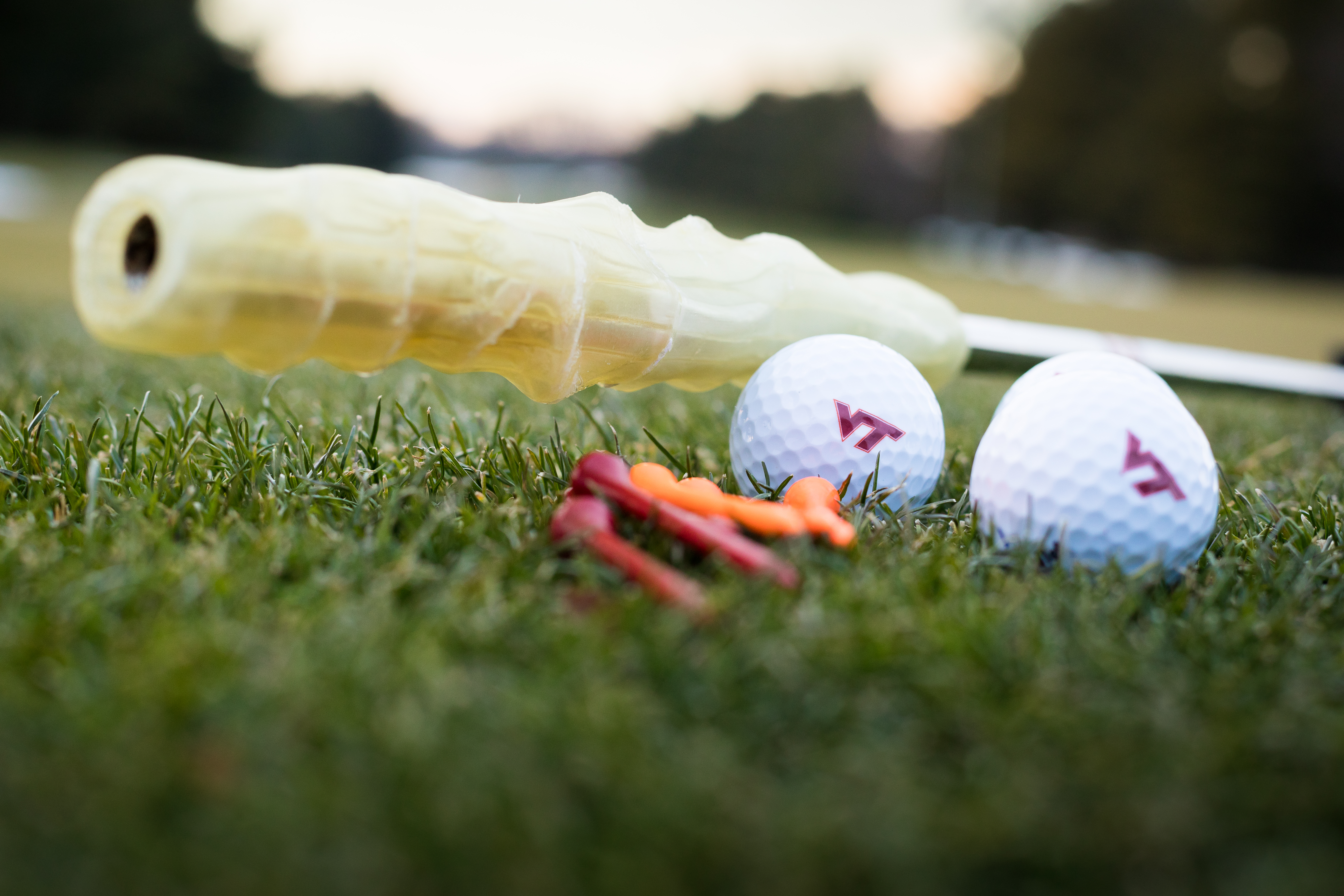
“We looked through the available literature on what people had printed before, and narrowed our choice of potential materials down to those with chemical similarities to what had been printed previously,” said Camden Chatham, macromolecular science and engineering doctoral student. “The thermoplastic polyurethane that we chose had never been printed before, so we had to perform a number of thermal and degradation analyses to make sure it would work.”
Thermoplastic polyurethane has been used for years to make automotive parts and other common tools, including medical devices. By converting the product into a filament for printing, the students were able to use customized structural infill patterns to tailor the stiffness of the grip to the golfer’s individual preference.
Chris Williams, an associate professor and the John R. Jones III Faculty Fellow of Mechanical Engineering, instructs the additive manufacturing course that inspired this team-based final project, challenging students to design a product that could be made using additive manufacturing.
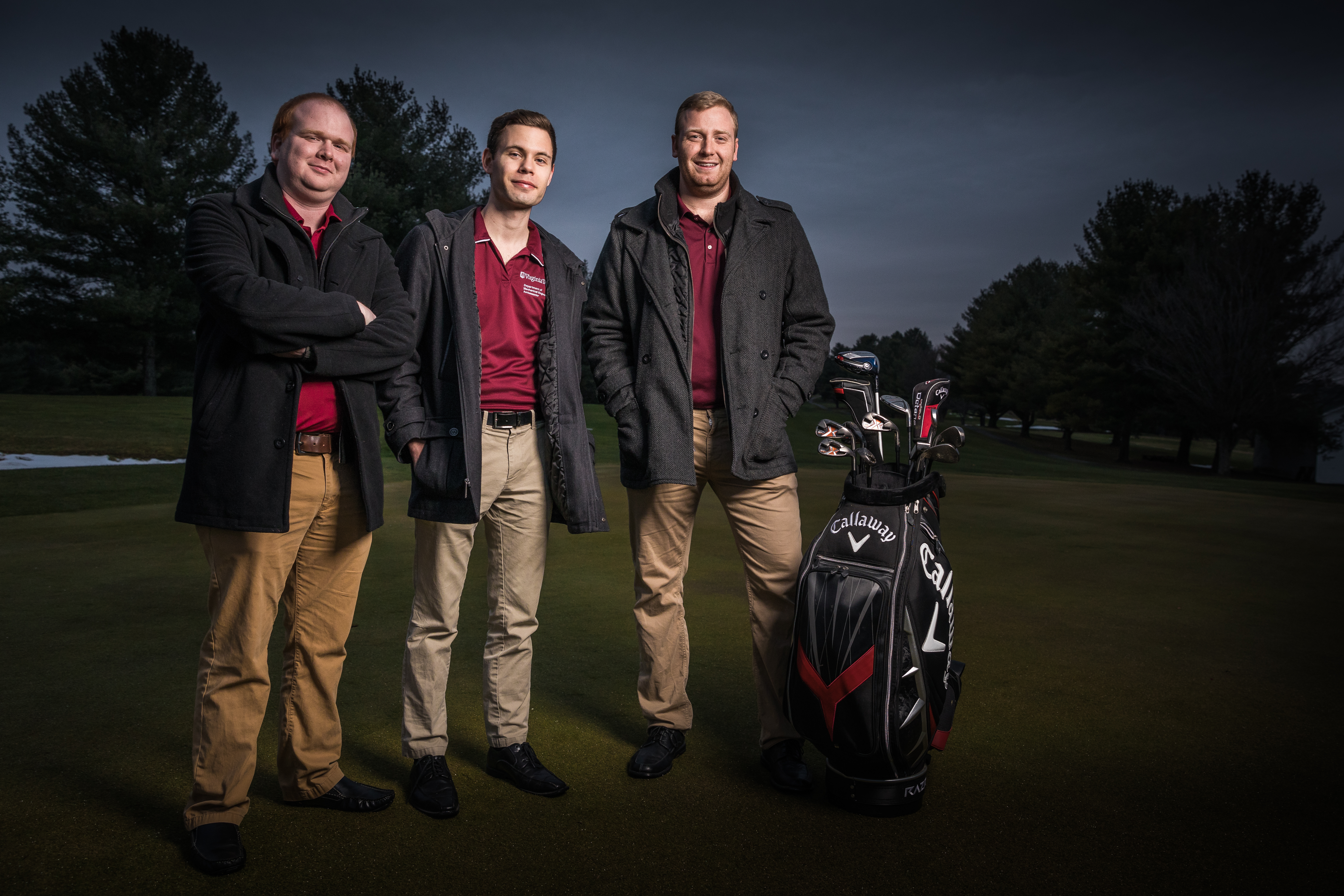
Through funding from ZinnStarter and the course challenge as motivation, Virginia Tech students designed the printable, flexible product to improve mobility for users.
The ZinnStarter accelerator program was created by Ray Zinn, the longest-serving CEO in Silicon Valley and the founder of Micrel Semiconductors, in partnership with Virginia Tech's Apex Systems Center for Innovation and Entrepreneurship. The program awards funding to college students pursuing innovative business ventures.
The Virginia Tech students garnered recognition with their design when they were awarded first place in the 2017 Society of Manufacturing Engineers’ Digital Manufacturing Challenge.
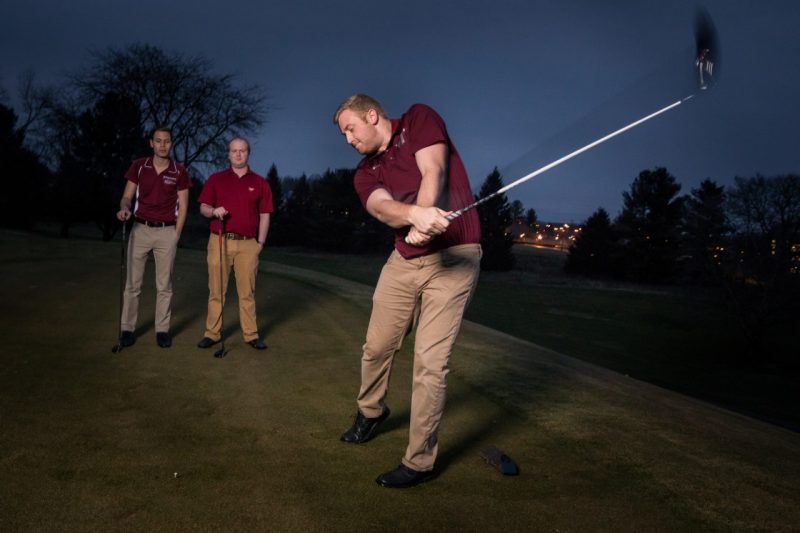
“From an educational standpoint, it was an excellent opportunity to correlate a class project with a competition,” Williams said. “From a research standpoint, this is the next generation. It’s not every day students come into class and say, ‘we’ve printed a completely a new product and we’ve done it using a material that’s never been printed before.' Because there were team members with polymer science and engineering backgrounds, they were able to modify an existing material to make something new.”
The winning team consisted of Chatham, a doctoral macromolecular science and engineering student, co-advised by Williams and Tim Long, professor of chemistry in the College of Science; Jacob Fallon, a doctoral macromolecular science and engineering student, advised by Michael Bortner, assistant professor of chemical engineering; Eric Gilmer, a doctoral chemical engineering student, advised by Bortner; and Andy Cohen, an undergraduate mechanical engineering student.
Kapton
Virginia Tech researchers created a novel way to 3-D print the type of high-temperature polymeric materials commonly used to insulate spacecraft and satellites from extreme heat and cold.
Previously, the polyimide could be made only in sheets.
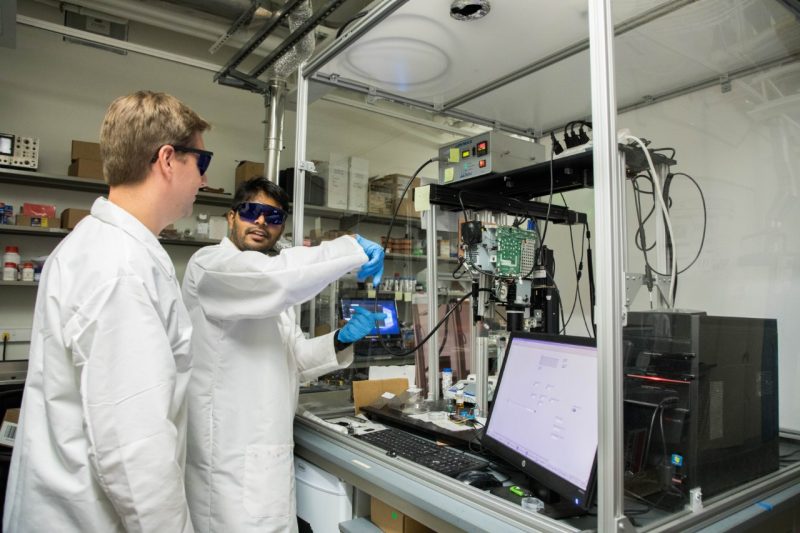
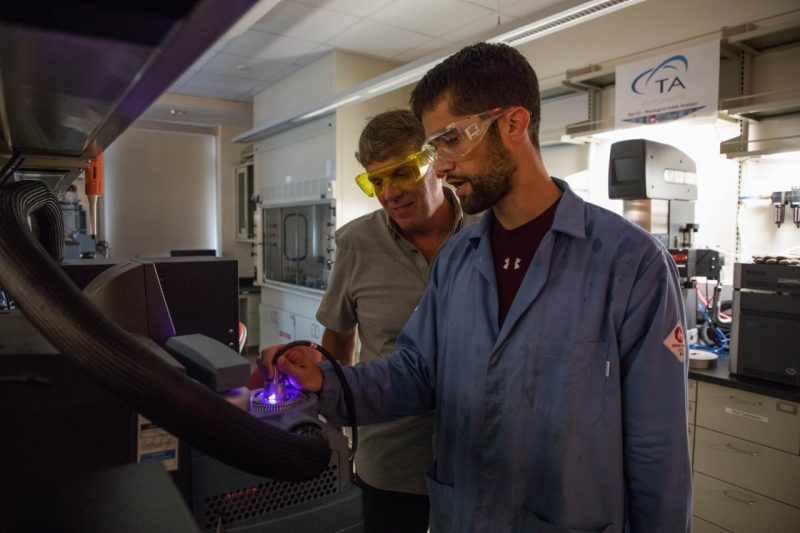
The material, formally known as Kapton, is an aromatic polymer composed of carbons and hydrogens inside benzene rings, which provides exceptional thermal and chemical stability. But because of this molecular structure, the material is notoriously difficult to produce in any format other than thin sheets.
Kapton often is used in the multi-layer insulation that forms the outer wrapping of spacecraft, satellites, and planetary rovers to protect them from extreme heat and cold. It often is mistaken for “gold foil.”
Researchers from the College of Engineering and College of Science were able to synthesize the macromolecules, allowing them to remain stable and maintain their thermal properties for processing in 3-D printing. The high-performance polymer now can theoretically be used in any shape, size, or structure, with small chess pieces and lattice bricks already produced inside Virginia Tech labs. Possible future uses are not limited to the aerospace industry. The same material can be found in scores of electronic devices, including cell phones and televisions.

“Conventional processing routes have limited engineers to make only thin films from these materials,” said Christopher Williams, an associate professor with the Department of Mechanical Engineering in the College of Engineering and leader of the Design, Research, and Education for Additive Manufacturing Systems (DREAMS) Laboratory. “Now that we can 3-D print these materials, we can start designing and printing them into much more complex 3-D shapes, which allows us to take advantage of their excellent properties over a much broader range of applications.”
Materials currently used in 3-D printing do not have the high strength and stiffness across broad hot-cold temperature ranges necessary for the extremes of space. Typically, printable polymers start to lose their mechanical strength at about 300 degrees Fahrenheit.
This new polymer maintains its properties above 680 degrees Fahrenheit, the research team said. “We are now able to print the highest temperature polymer ever—about 285 degrees Fahrenheit higher in deflection temperature than any other existing printable polymer. Additionally, our 3-D printed material has equivalent strength to the conventionally processed thin-film Kapton material,” said Williams, the Electro-Mechanical Corporation Senior Faculty Fellow in Advanced Manufacturing Systems.
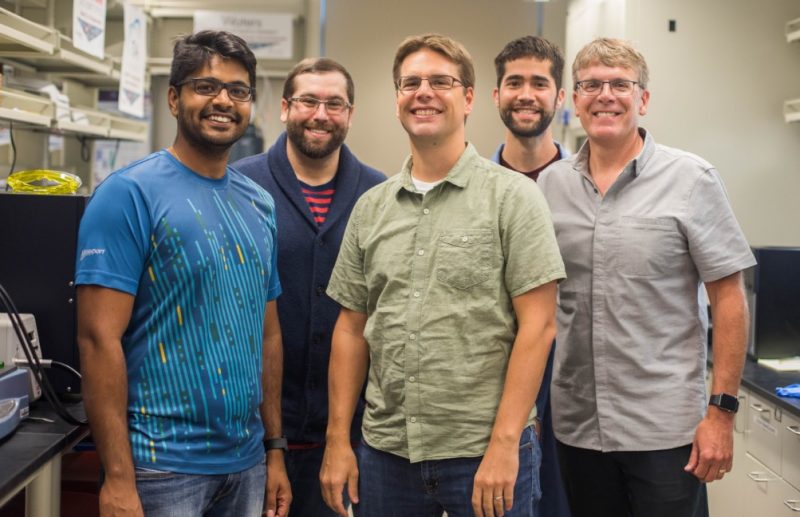
“We can imagine this being used for printing a satellite structure, serving as a high-temp filter or a high-temp flow nozzle,” Williams said. “We can imagine using the wide geometric and microscale possibilities offered by 3-D printing to further improve existing designs—say, a more lightweight satellite, a filter that provides optimum/efficient flow, a nozzle with a designed flow path that allows greater exit velocity and efficiency.”
A key early breakthrough in the project occurred in the laboratory of Timothy Long, a professor with the Department of Chemistry, part of the College of Science, and also the director of the Macromolecules Innovation Institute (MII), located within Virginia Tech’s Institute for Critical Technology and Applied Science. Williams is associate director of MII.
Long, working with then-post-doctorate researcher Maruti Hegde, now a research associate at the University of North Carolina at Chapel Hill, was exploring the possibility of making 3-D printed shapes from aromatic polymers, such as Kapton. The researchers, along with a graduate student team, were able to derive the novel polymer synthesis design, allowing the polyimide to be 3-D printed. Williams’ lab, led by College of Engineering doctoral students Viswanath Meenakshisundaram, of Bangalore, India, and Nicholas Chartrain, of Westfield, New Jersey, then exacted the process for 3-D printing.
“We chose a fairly ubiquitous high-temperature and high-strength polymer because we wanted to enable a rapid impact on existing technologies,” Long said, adding that being able to create such 3-D printed materials in any shape could serve a key market, such as the aerospace industry. Indeed, Long said companies have already shown early interest in the new material, which has a U.S. patent filed.
The two teams spent a year testing the material’s performance in extreme heat and cold temperature scenarios and fine-tuning how the material is machine printed. Williams’ and Long’s work recently was published in the Advanced Materials Journal under a fitting title: Processing the Nonprocessable.
Williams and Long have collaborated on numerous projects involving 3-D printing.
“At the end of the day, we are each other’s biggest cheerleaders,” Williams said of his work with Long’s lab in the College of Science. Long added, “We challenge each other with how polymer structures must be invented, or reinvented, to enable 3-D printing. We often joke that I am a post-doctorate researcher in the DREAMS lab and he is a post-doctorate researcher in my lab. It is truly a partnership for innovation.”
Lindsey Haugh, Steven Mackay, and Rosaire Bushey contributed to this story.
-
Article Item
-
Article Item